Case Study: Waste Oil and Filtration Sludge Incinerator Particulate Filtering using GORE Filter Bags
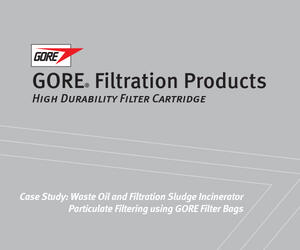
Case Studies, United States
The customer achieved a 30-month bag life with the first set of bags even though process upsets (electric failure, hopper fill-ups, leaking access door, etc.) occurred during the first 14 months of operation.
Application
Waste Oil and Filtration Sludge Incinerator. Three-module off-line pulse collector (546 bags). On demand cleaning is initiated at 6" w.g. every few hours. After one cleaning cycle, the DP is reduced to less than 3" w.g. The combustor is a rotating horizontal hearth which is used to fire a 50/50 mixture of filtration sludge and liquid. The liquid simulates #2 oil which contains phenols. The oil-like mixture produces approximately 2% ash. The flue gas contains fly ash and SO3. The baghouse operates with a flue gas volume of approximately 20,000 acfm (11,400 scfm) at 364ºF. The gas-to-cloth ratio is 2.0 (gross) and 3.01 (net).
Optimization Potential
Old baghouse using Teflon® felt filter bags had both high DP and particulate emission problems.
Solution
Gore worked with customer to design new baghouse parameters and install GORE® membrane/Teflon® B fiberglass fabric filter bags.
Results
The customer achieved a 30-month bag life with the first set of bags even though process upsets (electric failure, hopper fill-ups, leaking access door, etc.) occurred during the first 14 months of operation. Particulate emissions were recorded with an average concentration of 0.0089 gr/dscf, including condensibles. A substantial reduction in compressed air costs has been achieved. A second GORE® membrane filter bag set was installed in July 1990
FOR INDUSTRIAL USE ONLY.
Not for use in food, drug, cosmetic or medical device manufacturing, processing, or packaging operations