3 Baghouse Maintenance Mistakes That Can Cost You Money
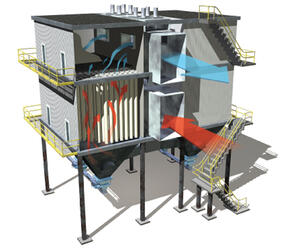
Technical Information, United States
Dust on dirty tube sheets can make it difficult to isolate the source of dust leaks. Be sure to thoroughly clean tube sheets before doing black light testing.
1. Make sure your pulse pipes are aligned properly over filter bags to prevent velocity damage and loss of cleaning effectiveness.
Pulse pipes can be knocked out of position during installation of replacement bags, during routine maintenance, or even when pipes were initially installed. Any of these errors could result in internal velocity abrasion and premature bag failure.
2. Keep hoppers clean and unobstructed.
Blocked hoppers cause a back-up of dust leading to velocity abrasion and premature bag wear. High dust levels in the hopper can cause high pressure drop from re-entrainment. High pressure drop results in higher energy costs, frequent cleaning and shorter bag life. Hoppers should be continuously evacuated and not used to store materials. If needed, install hopper level alarms or perform preventative maintenance on existing alarms to ensure proper function
3. Make sure bags and cages are optimally sized & constructed.
A mismatch between bag and cage sizes or between cage construction and stress points can cause premature failure due to localized wear points on the bag.
FOR INDUSTRIAL USE ONLY
Not for use in food, drug, cosmetic or medical device manufacturing, processing, or packaging operations.