GORE Magnet Wire for Oil & Gas Downhole Motors
Extend motor life, increase tool reliability and minimize the risk of unexpected catastrophic failures with durable magnet wire from Gore. With exceptional resistance to extreme downhole conditions, our robust wires are proven to maintain the highest voltage endurance — unmatched by traditional heavy build enameled wires.
Contact Us
United States
+1 800 356 4622
Germany
+49 9144 6010
+49 9144 6816 (fax)
UK
+44 1382 56 1511
+44 1382 56 1007 (fax)
Italy
+39 045 6209 209
+39 045 6209 165 (fax)
France
+33 1 5695 6565
+33 1 5695 6401 (fax)
Spain
+34 93 480 6900
+34 93 373 7850 (fax)
Sweden
+46 31 7067800
+46 31 864226 (fax)
China (Beijing)
+86 10 5707 4999
+86 10 5707 4900 (fax)
China (Shanghai)
+86 21 5172 8299
+86 21 6247 9199 (fax)
China (Shenzhen)
+86 755 8359 8262
+86 755 8359 1654 (fax)
South Korea
+82 2 393 3411
+82 2 393 1285 (fax)
Japan
+81 3 6746 2582
+81 3 6746 2571 (fax)
Overview
The oil and gas industry faces many challenges when drilling into the Earth at unprecedented depths to explore and extract underground resources. Traditional workaround methods to extend tool life, like installing wires with thicker insulation have proven ineffective against high temperatures and aggressive chemicals. All of which results in unexpected tool failures that are expensive to replace, shorter tool run-times, more maintenance/downtime and lost production.
Please contact Windings, Inc. to learn more about downhole motors featuring GORE Magnet Wire:
US Toll-free: 800 795 8533
sales@windings.com
www.windings.com
LONGER MOTOR LIFE, INCREASED TOOL RELIABILITY
GORE Magnet Wire is designed specifically to operate reliably in extreme oil and gas downhole environments, minimizing the risk of catastrophic failures for maximum tool-run times. Our mechanically robust wires have a unique engineered fluoropolymer insulation that’s exceptionally resistant to difficult conditions like chemicals, hydrolysis, and up to high pressure, high temperature (HPHT) environments.
MAXIMUM VOLTAGE ENDURANCE
We compared our magnet wire to a polyimide enameled wire using ASTM/NEMA MW 1000 test method. For both wires, we used the same AWG size with comparable insulation thicknesses. We tested the dielectric voltage breakdown after 12 days exposure to hydrolysis in 0.3% H2O and synthetic oil at 280°C.
Results showed that our magnet wire maintained maximum voltage endurance after continuous exposure to hydrolysis and harsh fluids at elevated temperatures. But, the polyimide enameled wire became brittle and cracked right away under mechanical stress. This type of wire lost its insulation resistance and voltage breakdown performance, which is unacceptable when trying to avoid tool failures, keep on schedule, and stay on budget.
GORE Magnet Wire is proven to provide durable mechanical protection and superior electrical performance continuously in severe downhole environments — extending motor life and increasing tool reliability for less risk of unexpected catastrophic failures.

Benefits
GORE Magnet Wire provides manufacturers with many benefits that improve electrical and mechanical performance such as:
- enhanced durability due to specialized insulation materials
- exceptional resistance to aggressive chemicals and hydrolysis
- superior electrical performance in wide-ranging temperatures up to 260°C
- proven highest voltage endurance in harshest downhole environments
- longer motor life and increased tool reliability
- minimize the risk of unexpected catastrophic failures
Please contact Windings, Inc. to learn more about downhole motors featuring GORE Magnet Wire:
US Toll-free: 800 795 8533
sales@windings.com
www.windings.com
Properties
These values demonstrate the electrical, mechanical and environmental performance of GORE Magnet Wire.
Property |
Value |
---|---|
Operating Voltage Range (V) AC | 300 — 600 |
Spark Test Voltage (V) AC | 1500 |
Dielectric Breakdown Voltage (kV) tested per ANSI/NEMA MW 1000a | 4.4 |
Wire Insulation | Engineered Fluoropolymer |
Conductor | Bare Copper |
Operating Temperature Range (°C) | -55 to +260 |
RoHS | Compliant |
a Testing based on size AWG 2801
Resources
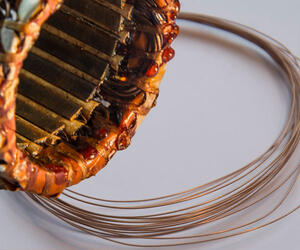
Data Sheet: GORE Magnet Wire for Oil and Gas Downhole Motors
Data Sheets, 831.01 KB
View all resources for Magnet Wire for Oil and Gas Downhole Motors
FOR INDUSTRIAL USE ONLY
Not for use in food, drug, cosmetic or medical device manufacturing, processing, or packaging operations.
Contact Us
Related Products
Cables & Cable Assemblies